What makes a Mountain Boat?
- mountainboats
- Feb 6, 2022
- 3 min read
So you might have noticed something different about our boats? The foundation of wood is the obvious answer but there are a few other wooden boat builders so what is the real difference?
TLDR; this article dives into the industrial processes that make a Mountain Boat, a combination of forgotten and new technologies that leave tradition behind, this distinct boatbuilding ethos brings out the advantages of wood without the cost of tradition.
It's always interesting to hear the polarisation on the topic of wooden boats, you are either aware of the advantages of wood or it represents everything bad and the idea offends you. People often offer to help me move a Pram around expecting a 'weight of a couple of hundred kilos' only to be shocked when they discover it weighs 35kgs.
The anti-wood sentiment is easy to understand as the art of building wooden boats hasn't progressed in over half a century. With the exception of a few traditionally built examples, this means that most people's wooden boat experience is based on second-hand boats ready for retirement.
The option of a new traditionally built wooden boat is not for everyone as the building process costs a fortune in labour. Despite the prohibitive cost, people that can afford it still choose a wooden boat as they know they are buying a quality boat. This is the central reason why we use wood as it provides one of the highest quality boats.
So how do we eliminate the prohibitive labour cost associated with tradition? This is where Mountain Boats differentiates itself by bringing industrial technology into the mix to provide the same boating outcome without the traditional price tag.
Above: build montage! Makes the whole process look so simple.
The story starts after the general shape and structure has been designed by a naval architect. With the help of Computer-Aided Design, the focus is now on how the parts are fabricated and come together. With many options on how to achieve this, the answer is usually the tenth attempt.
A CNC (Computer Numerical Control) router is an obvious choice to fabricate plywood parts that are accurate to the width of a human hair. The high accuracy of the parts allows for the inclusion of locating holes, notches and other subtle design features that then place these parts accurately into a jig that holds the components in their assembled form.
Plywood is nice but hardwood parts present a different problem as chunks of tree are clunky to use in a standard CNC router. As such these parts have to be fabricated by hand which takes skill and time to produce parts with far less accuracy than the adjacent plywood parts making the integration of parts tricky.
Initially, this stopped the idea of Mountain Boats dead in its tracks, dowels, lap joints and other common joinery techniques just didn't cut it. The time required to fabricate the parts with adequate accuracy was still more or less traditional wooden boat building and a chain is only as strong as its weakest link. In addition, the joinery methods convoluted the assembly process.

Above left: the first iteration, a simple pattern that would be replicated by hand and painful in the final assembly; Above right: the ~tenth iteration, fabricated in about 4 minutes and generally to +/- 0.1[mm].
Knowing that woodwork is as old as time a solution must already exist but where could we find a missing link that delivers the special sauce? Turning to Japenese carpentry for inspiration it didn't take long to identify better ways to design the parts to facilitate assembly however the fabrication was even more involved with labour.
Spinning around in circles and going off track we did what most people do to procrastinate, watch dumb things on Youtube. This session was all about fast things and the wooden wonder that is the De Havilland Mosquito (a really fast WWII fighter bomber aeroplane) came up in the playlist.
Mid-movie the gold was displayed in the form of a WWII war factory as a worker produced a part for the plane seamlessly with a router and template. Not a fancy process, just a simple solution that worked. The recipe for the secret source had been revealed and we got busy constructing a host of router templates to fabricate the boat's components. WWII technology to the rescue!
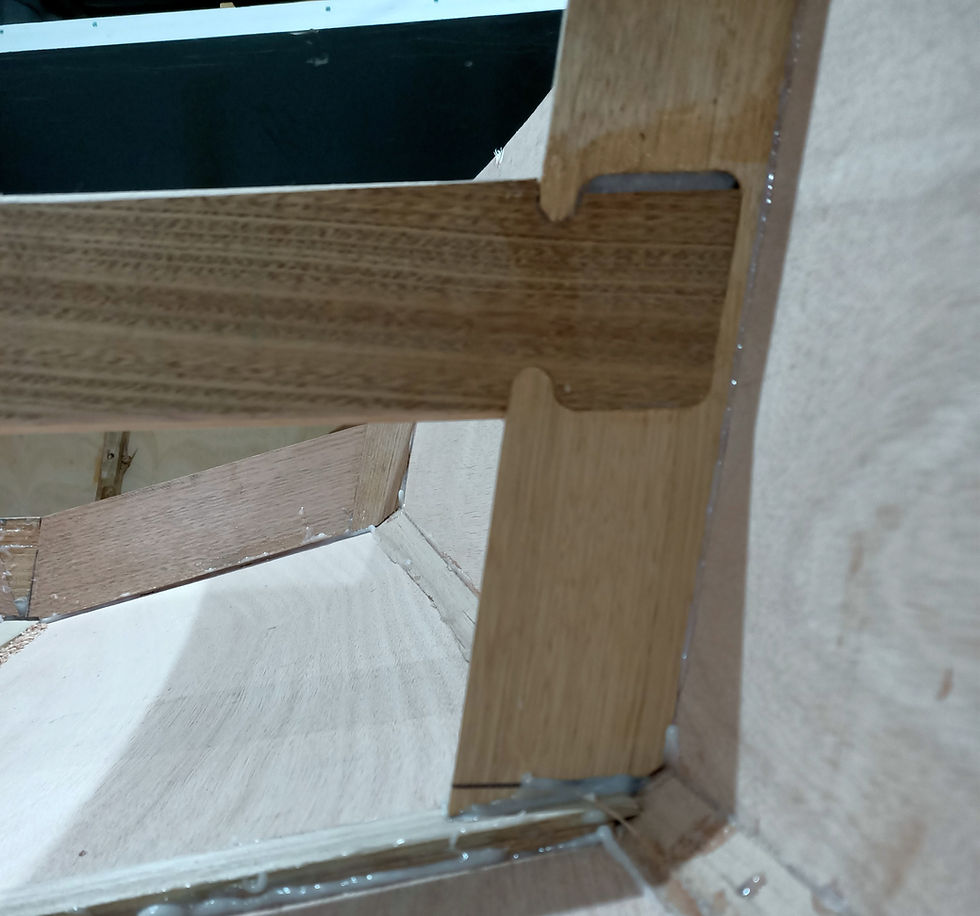
Above: The inspiration of Japanese carpentry, features like this make assembly a breeze.
With some refinement of the assembly process and a parts library filled with finely shaped wooden parts, the boats started flowing. Throw in a boat sized oven to accelerate the curing of glues and the 8' Pram became the first boat in over 50 years to fill the void of regular affordable wooden boats.
We have no intention of stopping the story there but that is the end of storytime for the moment. If you'd like a crystal ball to see the future of our boat building tech check out "firefly racing dinghy (1958)"...
Comments